Metal buildings are a popular selection for residential, commercial, agricultural, and industrial purposes this can durability, cost-effectiveness, and quick assembly. Whether you're erecting a garage, barn, warehouse, or workshop, understanding the metal building installation near me process is essential to ensure long-term performance and structural integrity.
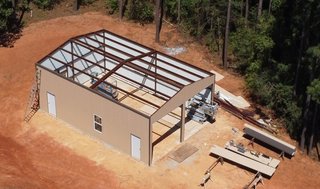
Benefits of Metal Buildings
Before diving in the installation process, it’s useful to understand why metal buildings are very widely used:
Durability: Steel structures can withstand extreme conditions, including high winds, heavy snow, and seismic activity.
Low Maintenance: Metal buildings require less upkeep compared to wood-framed structures.
Energy Efficiency: With proper insulation, metal buildings could be highly energy-efficient.
Customization: They may be tailored to specific needs, including dimensions, layout, doors, windows, and pallettes.
Quick Construction: Pre-engineered components reduce construction time significantly.
Step-by-Step Metal Building Installation
1. Site Preparation
Proper site preparation lays the foundation for a successful installation. This includes:
Clearing and leveling the land
Ensuring proper drainage
Pouring a concrete slab (if required)
Marking anchor bolt locations using the building's layout
2. Foundation Work
Most metal buildings need a concrete foundation. Depending on the structure’s size and purpose, this will likely include:
Perimeter footings
Slab-on-grade
Pier or trench foundations
Anchor bolts has to be set accurately during this phase to align using the base plates of the building frame.
3. Framing Assembly
The steel frame will be the backbone in the building. Installation starts off with:
Erecting the key frames (columns and rafters)
Connecting secondary framing elements like girts and purlins
Using cranes or lifts for heavy sections, particularly in large buildings
Precision is critical to be sure structural alignment and safety.
4. Installing Wall and Roof Panels
Once the frame is within place, metal panels are attached:
Wall panels are generally installed first
Roof panels follow, often including skylights or vents
Fasteners, sealants, and closures are used to ensure waterproofing and durability
5. Doors, Windows, and Trim
At this stage, openings are completed:
Roll-up, sliding, or walk-in doors are installed
Windows and ventilation systems are fitted
Trims and flashing are added for both aesthetics and weatherproofing
6. Insulation and Finishing Touches
If the dwelling is to be climate-controlled, insulation is added:
Foil-backed blanket insulation, rigid board, or spray foam are typical choices
Interior walls, electrical, HVAC, and plumbing systems are added as needed
Professional vs. DIY Installation
While some smaller metal buildings are available in DIY kits, larger or maybe more complex structures typically require professional installers. Licensed contractors ensure:
Code compliance
Safety and warranty protections
Efficient and accurate assembly
Installing a metallic building is a brilliant investment when performed correcly. Whether you're adding a garden workshop or building a commercial facility, knowing the installation process makes it possible to plan effectively and avoid costly mistakes. With proper preparation and execution, a metallic structure can last reliably for years.